Contact Plating Solutions for High Power Applications
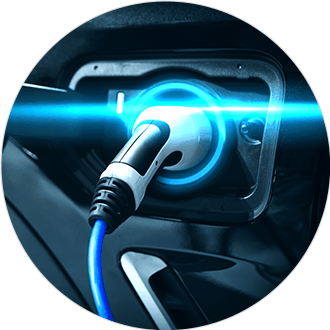
C100 Silver graphite dispersion is the newest and most noteworthy finish developed specifically for connectors. Unique self-lubricating dispersive technology provides excellent conductivity, and superior resistance to fretting corrosion, oxidation, vibration and high temperatures. Friction trace tests on C100 indicate low abrasion and no wear-through.
C100 achieves 10,000+ cycles without lubrication; end-of-life tests at 50,000 cycles confirm a low and stable coefficient of friction. Thermal aging shows stable tribological behavior and contact resistance at levels equal to pure silver. This gives C100 significant advantages compared with pure silver, as the latter provides lesser performance in terms of both wear and heat tolerance. C100 is cross-compatible with silver and silver alloys in the field.
Only a proven, well-documented silver dispersion coating such as C100 is capable of producing the reliable charging cycles and fast charging conditions required for high power connectors.
Indium 9100 (acidic) and 9200 (alkaline) are high-speed plating processes that deposit white, matte to semi-bright coatings that are RoHS compliant. In reflow applications, deposits are blister and void-free; whisker formation is exceptionally low compared to pure tin. Indium meets all requirements for press fit connections. Both processes have excellent cold-welding properties and are well-suited to low temperature soldering and thermal interconnects.
Sealing 691 is an organic antitarnish process based on nanotechnology: special nanopolymers absorb on the metal surface and crosslink to form a protective layer a few nanometers thick. Sealing 691 provides invisible protection from tarnish and wear, while preserving precious metal brightness.
Sealing 691’s aqueous formula is chrome-free and RoHS compliant. It will not compromise solderability or bonding capacity, has low contact resistance, and preserves metal's inherent lubricity, making it suitable for plug connectors and electrical contacts.
Miralloy® is a cost-effective alternative to silver, palladium and nickel for many connector and sensor applications. The newest Miralloy product, 2851, operates at 10 ASF, which is 25-43% faster than competitive products, providing substantial advantages in cycle time and cost.
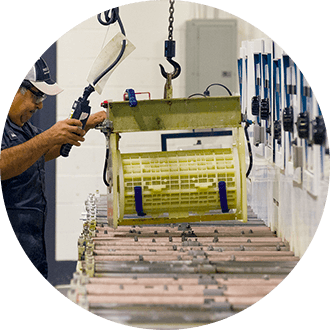
Miralloy is an advanced alloy that deposits up to 15 μm with exceptional uniformity. Its average composition is 51% copper, 33% tin and 17% zinc. Deposits resist abrasion and corrosion, and are non-magnetic, so they're well suited to high frequency applications.
Miralloy has earned widespread acceptance for use on HF connectors, contact elements and solder pins. It is plated using standard rack equipment.
NIPHOS® 968 – bright nickel-phosphorus alloy was developed to plate steel rods in hydraulics and shock absorbers: nickel-phosphorus layers are combined with chromium as a final layer. This combination allows lower thicknesses of the chromium and dramatically improves wear properties of the complete system. Niphos products generate huge energy savings as EN replacements, and exhibits less internal stress compared with existing nickel-phos electrolytes. Also available, Niphos 965 for reel-to-reel finishing.
Rhoduna-Alloy 1 is the world’s first galvanic rhodium alloy. It is a proven alternative to pure rhodium coatings, at a significantly lower cost. Formulated from rhodium and ruthenium, Rhoduna Alloy is a superior corrosion-resistant surface finish for the charging contacts and connectors used in mobile devices; it will not affect features such as fast charging capability.
Traditional gold-plated contacts corrode aggressively on contact with chloride-containing solutions, including perspiration, pool and sea water, and many beverages. In contrast, our rhodium ruthenium electrolyte gives mobile phones, tablets, wireless headphones and fitness wristbands a valuable measure of long-term durability.
Rhoduna Alloy deposits directly on a range of substrates, and exhibits good throwing power on intricate shapes. Deposit thickness can be modified easily; deposits are crack-free up to 1 μm.
MMO Anodes – or Mixed Metal Oxide Anodes, are manufactured from precious iridium and ruthenium oxides, sometimes combined with non-precious tantalum and titanium oxides. Solutions of these metals are applied in layers in a multi-stage process; they are subsequently transformed in a thermal process into their catalytically effective shape.